Supply Chain Management: It was the Best of Times;
It was the Worst of Times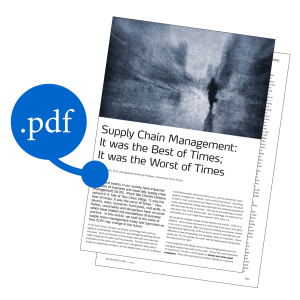
The recent events in our society have impacted all facets of business and especially supply chain management (SCM). Much like Charles Dickens opined in A Tale of Two Cities (1859), “it was the best of times; it was the worst of times.” Pandemics, wars, tsunamis, hurricanes, civil strife, inflation, uncertainty and disruptions have occurred which have shaken the foundations of business practice. In this article, we look at the state of supply chain management today and speculate on how SCM may change in the future.
In this brief article, the topics of people, technology, best practices, logistics, sustainability, infrastructure, and contingency planning will be discussed. Brief commentary on how things have been and how they might change for the better will be presented. The discussion will be predicated on the notion that supply chain management works well if things are happening normally or as they always have, but not so efficient and effective when abnormal events occur, such as pandemics, wars, weather emergencies, inflation, and currency fluctuations. According to ESRI in their 2023 Benchmark Report on the retail sector, the retail model assumed that change was predictable and achieving operational efficiency was the key to success. “As long as the world was a predictable place, that model worked well…but increasingly, the world isn’t as predictable as it once might have seemed.” (Esri 2023, p.1).
All disciplines undergo change as they develop and mature. SCM is no different. As a concept that was first mentioned in the 1970’s and 1980’s, it has come a long way. With omnichannel retailing and Internet marketing expanding significantly, SCM has had to become more efficient and effective to meet the growing, but changing, needs of customers. Some would say, “it’s not business as usual” with all these events taking place. And they would be right!
In the paragraphs that follow, some of these changing parameters for managing supply chains will be discussed. One of the continuing areas of importance in SCM is a firm’s ability to attract and retain good employees. More than two-thirds of retailers identify an important need to attract, hire and retain good employees (RSR Benchmark Report 2023). Bottom line is that there is not presently, nor anticipated within the next few years, enough people to fill all the logistics and supply chain entry level positions that will be available (Georgia Center of Innovation Logistics Education Report 2012). While more colleges and universities are starting or expanding their educational programs, there is insufficient capacity to generate enough people to fill those present and future SCM jobs. More faculty will be needed to teach logistics and supply chain courses. Of course, college students have to be motivated to choose SCM as a program of study. To increase the number of supply chain students in higher education, marketing such programs to students in the Kindergarten (K) through 12 grades will be necessary. Presently, that is a weakness in the educational system, and much more can be done to get these younger people interested in supply chain careers. Additionally, the various professional associations that offer certifications in logistics and supply chain topics could expand their programs to provide these options to students prior to them entering colleges and universities and before they enter the workforce. Some students would benefit greatly from obtaining certification in project management, analytics, transportation strategies, inventory control, forecasting, and other components of SCM. These programs could be more basic and elementary than what is being offered now by these groups but would provide a base of information on relevant SCM topics to allow new employees to be more productive and efficient in entry level positions.
With technology becoming very important in all facets of business, including SCM, it behooves companies to consider applications of artificial intelligence (AI), blockchain, electronic data interchange (EDI, forecasting, project management techniques, and a host of other digital approaches. There is consensus that technologies will continue to expand and find uses in industries that have historically implemented fewer technologies than firms in high-tech, pharmaceuticals, electronics, and others. Related to the educational aspect, colleges, universities and professional organizations must expand course offerings relating to the use of technology in SCM, establish specific analytics courses and provide hands on use of these technologies. To illustrate, knowing what a transportation management system (TMS) or warehouse management system (WMS) can do is NOT the same as using one of those systems. Too often, students are familiar with these technologies, but have little expertise in using them to make SCM decisions. This will require a reengineering of those logistics and SCM courses where those technologies are presented.
Logistics is the largest component of SCM and is primarily responsible for inventories, transportation, warehousing, sourcing, and many other basic functions of SCM. The uncertainties in the marketplace, especially those associated with COVID (2020-2022), have highlighted the need for transparency, resiliency, agility and rapid decision-making. As a result, firms have had to re-examine areas of their business where “business as usual” was the norm. However, when COVID caused significant replenishment issues in many industries, it was the firms that had more inventory that had more product to sell when sources of supply were reduced. Similarly, high customer service levels require more inventory, but when sources of supply are limited, firms may not be able to adjust quickly (locating new suppliers, stocking up on extra inventory). Most logistics systems have been in place for quite a while and under normal circumstances run very efficiently and effectively. However, when normal is no longer the norm, firms need to re-assess their inventory management strategies and perhaps hold more inventory/safety stocks, or they may have to reduce customer service based on lower inventory levels, or change from outsourcing from distant markets to near sourcing or local sourcing to allow products to be procured faster. One example is when a firm utilizes a Just-in-time (JIT) strategy. Very little safety stock is maintained since the firm depends on its suppliers to deliver quickly and in the right amounts. When the normal does not occur, JIT becomes a problem because stockouts do occur. Similarly, sole sourcing is a great approach to use when building vendor loyalty, consistent service, and high quality. However, if that single source goes offline due to some weather calamity, etc. it may be difficult to obtain another supplier quickly. One approach that is used in the automobile industry is to create car parks where the automobile producer is located there, plus the major suppliers. Having all or most supply chain members in one location in close proximity to one another eliminates a lot of uncertainty and likely reduces supply chain costs and potential service disruptions. The approach certainly increases supply chain visibility and agility given the location of suppliers and vendors near the manufacturer. The concept could have potential applications outside the manufacturing sector.
Sustainability issues continue to be a priority for organizations of all types. Examples include ethical sourcing, carbon neutrality, social responsibility with respect to employees and customers, environmental aspects, and many more. Firms have been developing strategies and tactics to improve their ESG efforts, but more is needed on a selective basis. Decisions regarding sustainability initiatives require full understanding of life cycle assessment, life cycle costing and cost-benefit analysis. There are costs and benefits to all strategies and tactics and firms need to consider both when deciding what approaches, they should take regarding sustainability. Clean energy solutions are not easy decisions to make. Electric vehicles are all the rage today, but there are other options such as hydrogen, biomass, synthetic fuels, etc. Each solution has both pros and cons that need to be considered and firms must exam the ROI of each potential option. Are solar panels the best option for a warehouse or manufacturing plant in a firm that is in a geographic region that has little sunlight? Are windmills options in Florida if the average wind speed is less the 5 mph? What are the cost-benefit trade-offs? These are difficult questions to answer without data and the expertise to understand that data. With respect to labor issues, especially in foreign markets, firms need to keep abreast of working conditions, age of workers, the environments in which those employees work, benefits provided to workers, and many more HR issues. While low cost for labor has consistently been a factor when selecting international locations for manufacturing and distribution, should low costs be the dominant factor, or should other attributes be given higher priorities? Difficult decisions, especially when the decisions impact costs and profits.
Existing infrastructure within the USA and throughout much of the industrialized world, are showing signs of decay. Like people, roads, bridges, ports, etc. get older and they slow down; that is, travel over the infrastructure takes longer. While governments are primarily responsible for financing expanded highway systems, new and renovated bridges, and larger airport, ports, and pipelines that allow logistics and supply chain activities to flow more smoothly and efficiently, that does not mean the industries and the companies that utilize them should just wait until governmental bodies take the initiative to upgrade or replace existing infrastructure. Being proactive with government agencies, industry associations, government officials and other entities that influence infrastructure improvements is a necessity. Organizations should be proactive in identifying needed infrastructure improvements and use lobbying efforts, industry presentations and press releases to educate the public and government officials about those needed improvements.
Contingency planning has been a staple of supply chain education for decades, but just having plans on how to prepare for a disruption is no longer sufficient. Traditional contingency planning is sporadic, while market conditions require that planning be continuous. Organizations cannot always predict what will occur in the future that might adversely impact their operations but having a good contingency plan coupled with a visible and transparent supply chain, will allow firms to respond more quickly, efficiently and effectively to those changing conditions. To illustrate, a regional company in the Florida area that sells and distributes alcoholic beverages, underwent a contingency planning exercise prior to the pandemic. At the time, COVID was unknown to them; they merely were trying to prepare for certain future eventualities that could negatively impact their business and customers. Part of the planning process was to identify additional vendors/suppliers that could fulfill their orders for various beer, wine and other alcoholic beverages. Rather than just identifying a need to have additional vendors/suppliers “just-in-case,” they specifically identified those companies and made initial contacts with those in critical areas of supply. When the pandemic occurred, the company had already performed the initial search and identification of alternative suppliers/vendors, and it was much easier and faster to transition to those new suppliers. Presently, the company continues an ongoing program of contingency planning relative to future potential supply chain disruptions. Other approaches to contingency planning are also possible. One very large company in the electronics/technology area will not use any sole sources for their critical supplies. Typically, they have 2-3 suppliers/vendors with whom they do business on a regular basis, thus reducing the downside risk of a major supplier not being able to fulfill orders.
In sum, organizations can minimize risks associated with uncertainties and disruptions, but they can’t eliminate those risks. They can prepare for those risks and minimize the problems that often arise when market conditions make it more difficult to carry on “business as usual.” As a young person involved in the Boy Scouts, I learned the Boy Scout motto: Be prepared! It’s a great motto for supply chain executives as they and their companies face more uncertainties and risks in the future. For firms that respond appropriately, it can be the “best of times.”
__________________________________
References
“Supply & Demand of Logistics Workforce and Education” (October 2012), Georgia Center of Innovation Logistics Education Report
Kilcourse, Brian and Steve Rowen (August 2023), “Agility, Resiliency, and Sustainability as a Strategy in Consumer-facing Businesses, Benchmark Report, ESRI.
“The Quest for a Resilient and Agile Supply Network” (April 2023), RSR Benchmark Report.
Stock, James R. (2013), “Supply Chain Management: A Look Back, a Look Ahead,” CSCMP Supply Chain Quarterly, pp. 30-34. https://www.supplychainquarterly.com/articles/739-supply-chain-management-a-look-back-a-look-ahead